- Messages
- 14
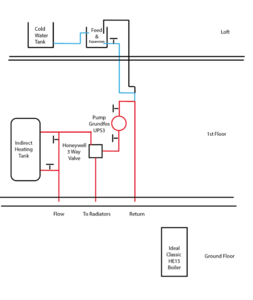
Initially one small radiator wasn't performing as well but the bearings on the pump were on the way out, as was the 3 way valve, so they have been replaced, system left for 2 weeks with X800 and cleared out again (every system drain looked clean) and filled with x100.
That rad is now better, but the out pipe doesn't get as hot, and the rad isn't baking like the others. However, I can't find the manifolds and popping up the carpets isn't an option at the moment.
Since we've had the work done though (and possibly before as we haven't been in long) there seems to be a lot of air in the system, especially in the HW circuit rather than the CH.
All rads have been bled ok.
What we are finding is that when the HW is on, there is a lot of air noise in the main flow / return pipe. I can't seem to bleed the air out as there is no nipple valve on that circuit.
But what I have noticed is that the system expands a lot, and tends to push through the cold feed (thinner pipe) instead of using the expansion pipe (thicker).
See the diagram to show how they all link together.
Also what I have noticed, which is maybe how the air is pulling in, is whenever the HW turns off, there is a jet of water pushed into the F&E tank.
I know this because if I close the feed, water pushes out of the expansion when you turn off the HW. Usually you just see the movement in the tank from where it's coming back up the feed pipe.
On the whole, the system works fine. No knocking, more air flow noises, and drip noises in the boiler and the odd rad.
I've tried lowering the water level in the F&E and bending the ball arm, but tbh could only drop it by maybe 2 inches but it is less than half full now.
The other thing to note is that the boiler only stays on for around 2 minutes then shuts off for maybe 4 and goes back to the same. It doesn't seem to stop teh rads or water getting hot, but in case it relates to anything?
Any other tips, as I can't really get a plumber in right now I guess.